Ryukyu indigo and indigo dyeing
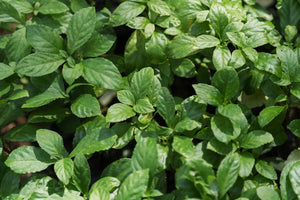
About Indigo
"Ai" is the Japanese name for the color ‘indigo’, which is translated into English as ‘indigo’. Humans have been extracting pigments from plants since ancient times. In Japan, there are several plants that have indigo pigments, such as Indian indigo (Fabaceae), Daqing (Brassicaceae), Tade (Polygonaceae), and Ryukyu indigo (Lepidoptera).
Ryukyu indigo” was cultivated from India to the Indochina Peninsula, southern China, Taiwan, Okinawa, and western Japan such as Kagoshima and Shizuoka until the Meiji era. As the times changed, chemical dyes were widely distributed, and natural indigo dye was gradually eliminated because of the time and effort required to produce it. Currently, “Ryukyu indigo” is grown almost exclusively in Okinawa and has become a precious commodity.
Production Method of Dyes
The vibrant blue pigment emerges by force of nature from colorless components.
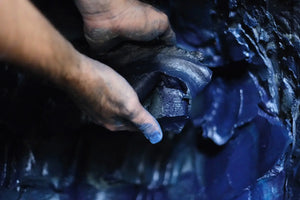
Precipitation Method
The harvested indigo leaves and stems are soaked in water to extract the pigment components.As the soaked indigo leaves ferment, the indigo pigment called indikan dissolves into the water and is decomposed into indoxyl. When the leaves are sufficiently extracted, they are pulled up, collected, and mixed with shellfish ash or slaked lime and aerated to purify the indigo pigment (indigo).
The indigo pigment is separated from the plant residue and precipitated out only as a paste-like mass of watery pigment (precipitated indigo, called muddy indigo in Okinawa).
Precipitated indigo has a high content of indigo pigment and has been used since BC, and is said to be the oldest dye-making process in the world.
Process of Producing Ryukyu Indigo Dye
-
Loading image: We begin by growing the seedlings.
Although Ryukyu indigo is an Okinawan variety, it is sensitive to ultraviolet rays and cannot be grown in the strong direct sunlight of Okinawa, making it very delicate.
It is very delicate and cannot be grown in the strong direct sunlight of Okinawa. It must be grown in an obliquely lit environment or it will die.
(Planting begins in November, and harvesting is at its peak during the rainy season in May and June of the following year.) -
Loading image: The grown seedlings are planted in the field.
The Ryukyu indigo seedlings, which have been fully grown in the greenhouse for about two months, are planted in the field.
The fields in which the seedlings are planted must have the same slanting light environment as the seedlings.
If there is no sunlight at all, the plants will not grow well, and if the sunlight is too strong, they will wither and die, so we are very careful to find a balance between shade and sunlight.
-
Loading image: Hundreds of kilograms of harvested indigo leaves are transported for soaking
The rainy season in May marks the beginning of the reaping season. Ryukyu indigo grows faster during the rainy season. In Okinawa, after the rainy season is over, it becomes midsummer in July, when ultraviolet rays become very strong, so the reaping is completed during the rainy season.Immediately after harvesting, the harvested Ryukyu indigo leaves are soaked in a soaking tank filled with a large amount of water.
Only about 10% to 15% of the indigo leaves can be extracted for dyeing.
The process is very physically demanding, as the indigo leaves are harvested and produced again immediately after the production is completed in order to stockpile the precipitated indigo to be used throughout the year.
-
Loading image: The harvested indigo leaves are soaked in water and fermented, waiting for the pigment components to be extracted from the leaves and stems.
As time goes by, the pigment components are gradually extracted from the soaked Ryukyu indigo. The soaking time varies depending on the air and water temperatures, so it is important to keep a close eye on the soaking process.
Because Okinawa has a tropical climate, the temperature is high even in May and June, and the speed of fermentation is so fast that if we make a mistake in judgment, overfermentation will occur and the pigment will decompose, making it impossible to extract the pigment from the soaked indigo leaves.
-
Loading image: Once we have extracted enough pigment components from the indigo leaves, we remove the spent leaves.
Immediately after the indigo leaves are removed, a very beautiful emerald green liquid is floating in the air.
The timing of this pulling is very important because it depends on the temperature of the water and the temperature of the air. The fermentation speed can be fast or slow, and it is difficult to adjust.
-
Loading image: Shellfish ash is dissolved in water and poured in.
Dissolve the shellfish ash in water and add it to the mixture to create a highly alkaline condition.
If the amount is wrong, the Ph level may not rise sufficiently, so the amount should be sufficient for the weight of the soaked indigo leaves.
-
Loading image: After feeding, agitate for a while to let air in.
Shellfish ash is fed in and stirred for a while while the Ph level rises sufficiently to feed air into the system.
-
Loading image: " The pigment components, once exposed to air, begin to transform the liquid into a blue hue, gradually forming blue bubbles."
By stirring, the extracted Ryukyu indigo pigment component and oxygen combine and the emerald green liquid gradually turns blue and turns into a blue liquid.
Air bubbles are generated in the process of feeding air into the water, so the surface of the water is covered with indigo bubbles.
-
Loading image: Once the bubbles dissipate, we allow the pigment to settle, concluding the stirring process. The following day.
After stirring for a while, the number of bubbles gradually decreases. When the bubbles are gone and the surface of the water is calm, sufficient pigment has been produced.
-
Loading image: After removing the supernatant, the precipitated pigment components are transferred to a cloth-laid container to drain off the water while removing the impurities.
Once sufficient indigos are produced, after a short time the pigment components precipitate to the bottom and separate into the pigment and the highly alkaline supernatant water. Only the supernatant water is removed and the precipitated dye is transferred to a cloth-lined container and allowed to drain off the unwanted water for several days.
-
Loading image: Ryukyu indigo is transformed into a solid pigment block, known as "precipitated indigo," derived from the plant's leaves.
This comprehensive process involves cultivating the fields, growing the plants, harvesting, manually producing precipitated indigo, and then dyeing yarns and fabrics to craft products. While creating precipitated indigo is time-intensive, its particles struggle to penetrate yarn or fabric in this form, making direct dyeing ineffective. To effectively dye, the indigo must undergo fermentation with the help of microorganisms in the subsequent step, turning it into a viable dye.
Fermenting Indigo into Dye
-
Loading image: The precipitated indigo is soaked and dissolved in water while removing the impurities.
The produced muddy indigo (precipitated indigo) is dissolved in water and passed over a colander to remove impurities. After dissolving in water for a while, it is separated into the indigo pigment and the supernatant layer.
Since the pH value is high due to the use of shellfish ash in the indigo production process, the supernatant is replaced and the process is repeated for several days to remove excess scum to obtain a pH value suitable for indigo production.
-
Loading image: We monitor the supernatant's condition and assess its pH level and water temperature, which indicates the concentration of hydrogen ions.
The pH value is an abbreviation for hydrogen ion concentration (Potential Hydrogen). Indigo dye is called an adhesive dye, which adheres to fibers.
Under normal conditions, it is insoluble in water and does not easily adhere to fibers. In the process of metabolism by microorganisms (reducing bacteria) that grow in an alkaline environment, it changes from insoluble to water-soluble and becomes soluble in water.
Therefore, indigo dye must always maintain a constant high pH value. In Okinawa, the reduction bacterium is propagated by adding syrup and awamori (Okinawa rice wine) to the indigo every day while monitoring the mood of the indigo.
Since only a limited number of reducing bacteria can grow in an alkaline solution, maintaining a high alkaline state and optimal temperature prevents the growth of bacteria other than the indigo reducing bacteria.
-
Loading image: The precipitated indigo must be stirred twice daily, in the morning and evening, to prevent it from decomposing.
As the number of reducing bacteria increases and metabolism becomes more active, the pH value decreases because acid is simultaneously generated in the metabolic process.
As the pH level drops, other bacteria can easily multiply. As other bacteria multiply, the pH value drops rapidly and the dye solution becomes oxidized, making it impossible to dye.
When the number of bacteria increases, the dye solution becomes more acidic, so we adjust the pH value with shellfish ash to keep the dye solution alkaline.
-
Loading image: We check and adjust the condition of the dye every day and keep it fermenting little by little, day after day.
The buzzing bubbles that accumulate in the supernatant of the dye are called “indigo flowers” and are one of the barometers that the dye is fermenting well. It is used as a guide to determine whether or not indigo building is progressing.
As fermentation progresses, the color of the dye gradually changes from blue to green.
-
Loading image: We test dye to check the coloration before dyeing a piece. Indigo produces a blue color when it comes in contact with air.
When the cloth is soaked in the dye solution that has fermented and is ready to be dyed, the fabric has a greenish color, but it gradually turns indigo when exposed to air. When the cloth is sufficiently dyed, indigo building is completed.
-
Loading image: Once the indigo construction is completed, it is time to start dyeing the work.
Indigo develops color by oxidizing when exposed to air. Therefore, when the fabric is soaked in the dye solution, the air must be removed properly or it tends to become uneven.
-
Loading image: The fabric is dyed and exposed to air to check the color and then dyed over and over again to produce an even more beautiful indigo color.
In order to produce a beautiful indigo color, the indigo is dyed over and over again. Checking the concentration and finish of dyeing each time, we find that even if the dye is placed in the same dye solution for the same amount of time, if the temperature and weather are different, the dyeing process, hue, and concentration will be completely different. Unlike chemical dyes, which can be used to dye several identical items, there are areas where it is difficult to achieve the same result even if you aim for it. Indigo dyeing is truly a “once-in-a-lifetime color.
-
Loading image: Once the color has been dyed to a satisfactory level, the fabric is thoroughly hand washed to remove excess dye.
After dyeing, the fabric is rinsed several times to remove excess dye.
After washing thoroughly, dewatering, and drying, check the color when it is dry. If a darker color is desired, the fabric is re-dyed.
-
Loading image: To finish, the fabric is placed in the sun to scorch excess dye.
After checking the color when it is dry, place it in the sun on a sunny day. Indigo pigments are decomposed when exposed to ultraviolet light, so the UV rays scorch the pigments that have not been firmly adsorbed onto the fiber.
-
Loading image: After drying in the sun, soak in hot water to remove the scum.
Finish by soaking in hot water at 40~45 degrees Celsius. The brown scum will gradually come out after soaking in hot water.
After soaking in hot water for about 2 hours to remove the scum, lightly rinse in cold water and dry again.
Drying in the sun and removing the scum are essential processes to keep the beautiful color for a long time.
-
Loading image: This dyeing method takes a lot of time and effort, but at last, we have a unique "Ryukyu Blue" that can only be produced by Ryukyu indigo dyeing.
The coloring of Ryukyu indigo, which is created by taking time, is completed entirely by hand. It takes a long time to cultivate the plants, produce the dye, and dye the fabric, but no part of the dyeing process can be omitted.
However, we believe that the color has its own charm, and we would like to share the “RYUKYU BLUE®” produced from Ryukyu indigo with as many people as possible.